
References
RockFeel hat nicht nur Ideen. Wir haben unsere Sensoren und Geräte in realen Einsatzfeldern getestet. Übertage und untertage. An Gestein und Beton. Viele Stunden. Läuft.
- Validierung am stationären Teststand HXS1000-50 TU Freiberg
- Tests in Steinbrüchen – Anbaufräse in Porphyr, Sandstein, Andesit
- Mobiler Teststand Freiberg – Anbaufräse auf Massivbeton
- Tests untertage – Teilschnittmaschine im Steinsalz
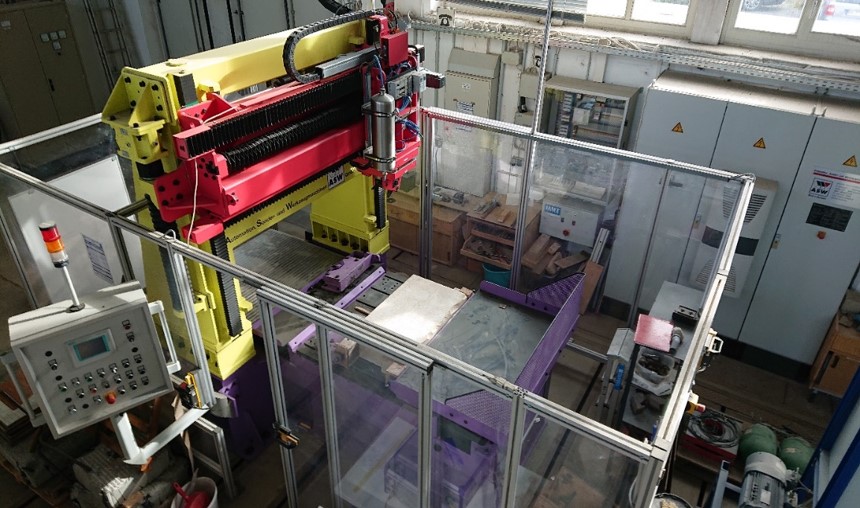
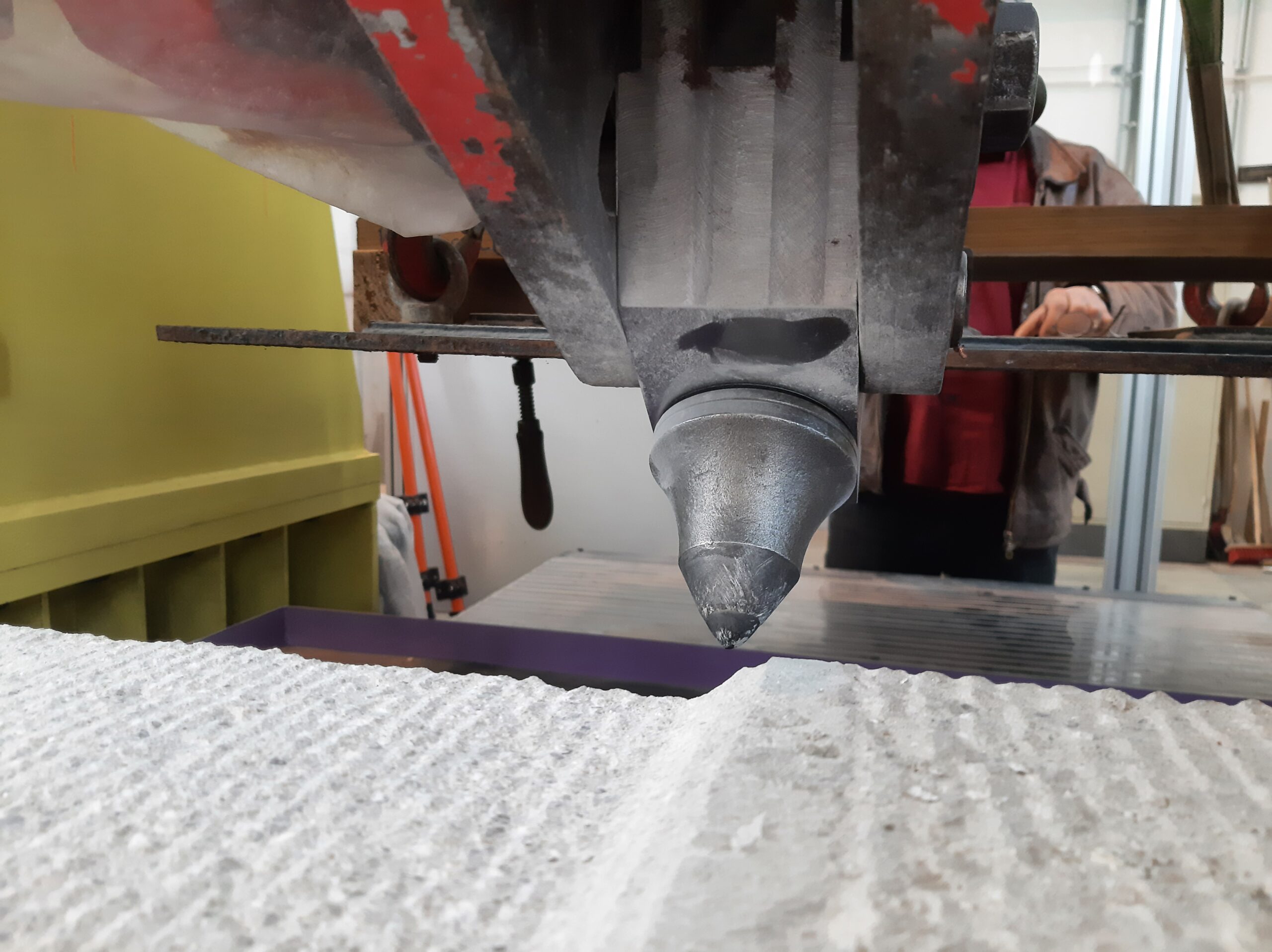
TEST AM Schneidversuchsstand
Validierung mit Betonproben
Das Funktionsprinzip der RockFeel-Meißelsensorik wurde 2021 auf dem stationären Teststand HXS1000-50 am Institut für Bergbau und Spezialtiefbau validiert. Mit dem teststand können Blöcke von 100x60x50cm mit einem feststehenden Meißel unter exakt definierten Bedingungen hinsichtlich Anstellwinkeln und Schneidparametern geschnitten werden. RockFeel hat Probekörper aus jeweils zwei verschieden festen Schichten Beton (UCS 15 |22|40MPa) geschnitten und die Meißelbewegungen während des Schneidens vermessen.
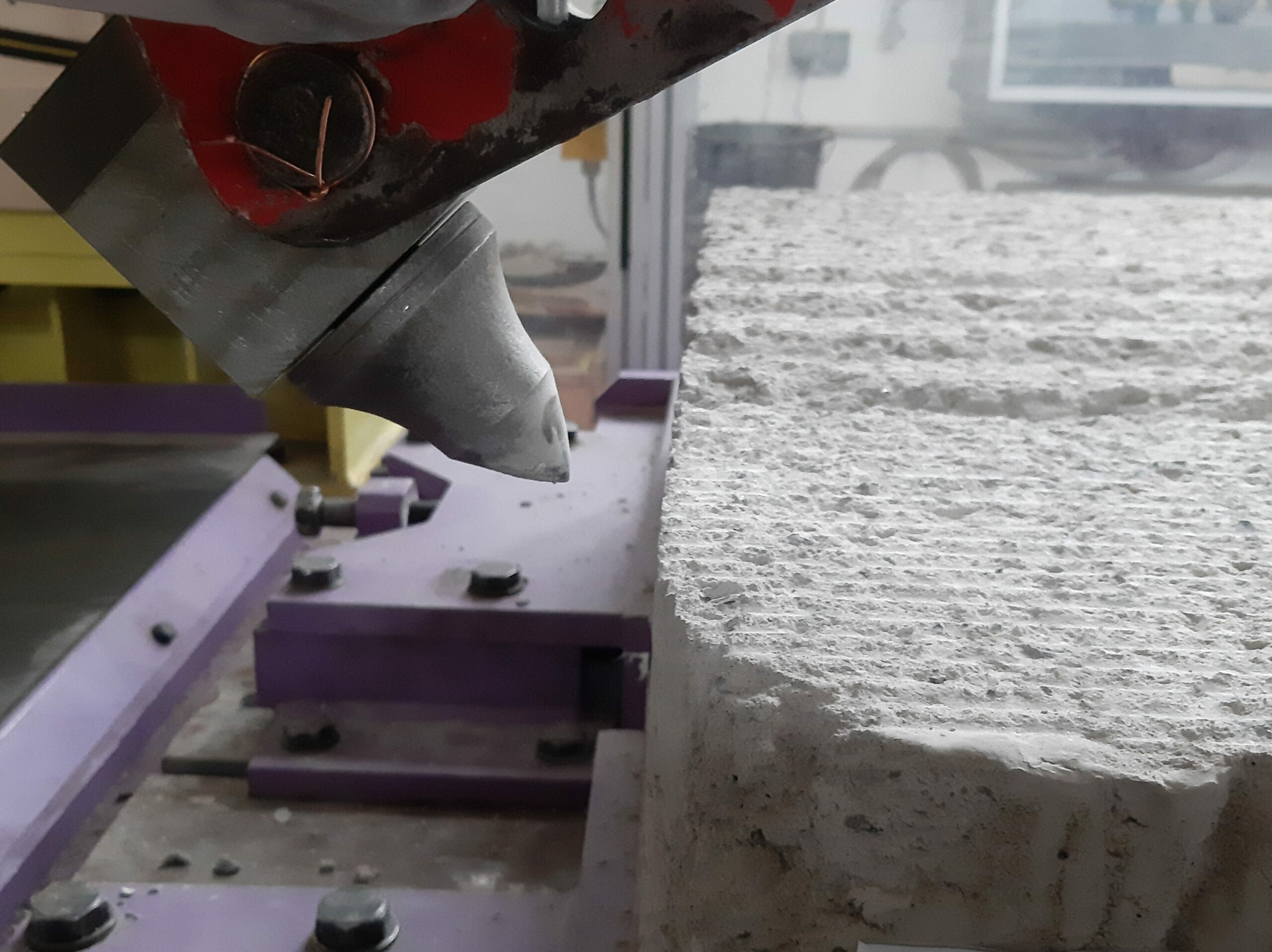
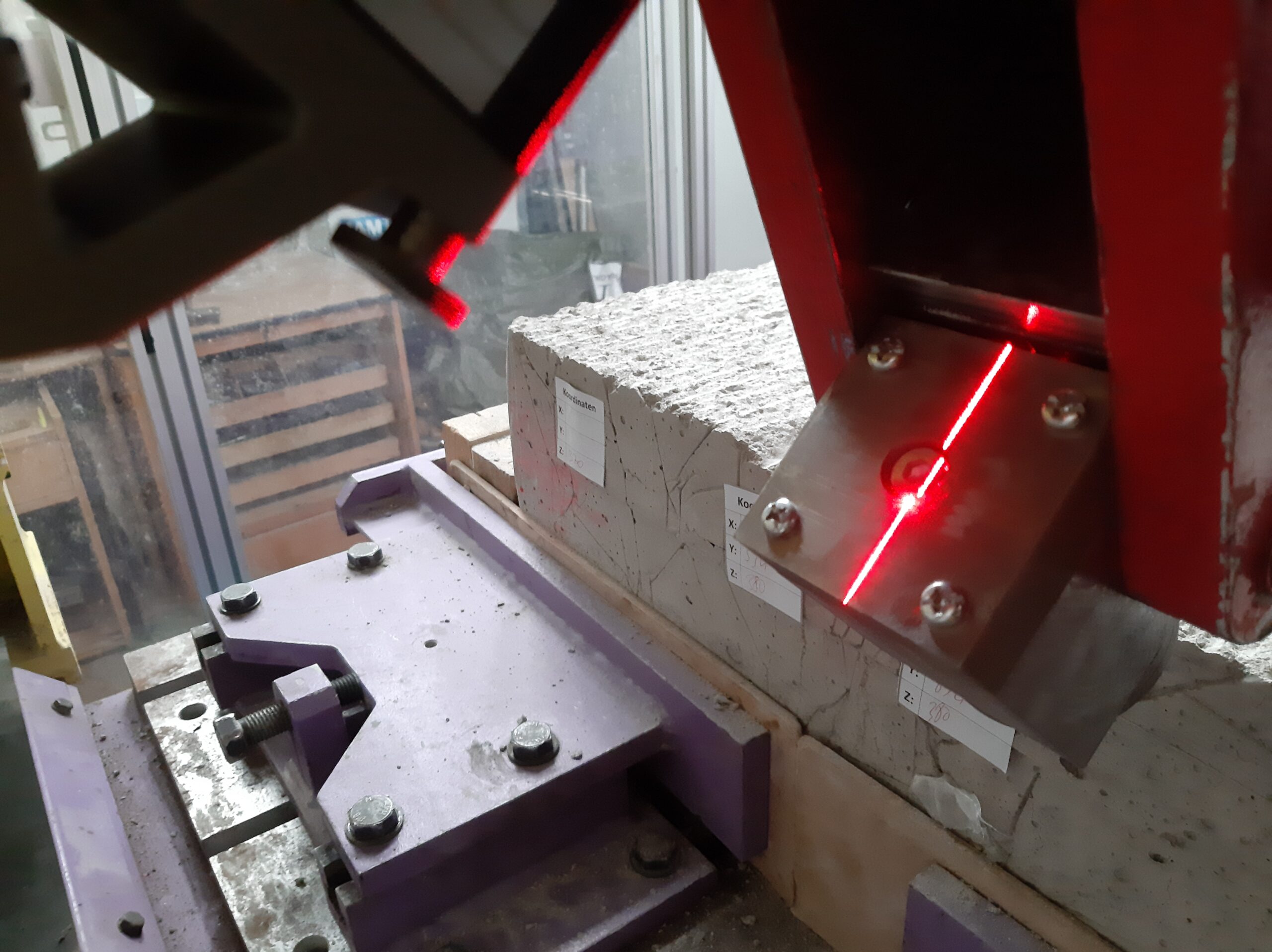
Als Referenzmessystem wurde ein hochauflösender und schneller Laserprofilscanner von Keyence eingesetzt, der frei schwebend hinter dem Meißel montiert wurde, um die Relativbewegungen des Meißels im Halter parallel zu den im Halter verbauten Sensorsystemen unter Test sehr genau zu vermessen, ohne ihn durch die extremen Erschütterungen während des Schneidens zu zerstören. Parallel wurden die Schneidkräfte aufgezeichnet. Die Erschütterungen beim Schneiden übertragen sich erheblich bis auf den Hallenboden. Der Laser wurde mit einem Beschleunigungssensor von Micro-Epsilon verbunden, der sogar die Luftschallkopplung vom Meißelhalter erfasste, um sicherzugehen, dass Sekundärschwingungen des Versuchsstands die Ergebnisse nicht verfälschen. Vorrichtung und Verfahren wurden nach der erfolgreichen Validierung zum Patent angemeldet.
Neben der RockFeel-Sensorik wurden Beschleunigungssensoren und Dehnmessstreifen auf dem Meißelhalter getestet, die jedoch den Belastungen nicht standhielten oder – wie zu erwarten – inkonsistente Ergebnisse lieferten. Das gleiche Ergebnis ergab sich bei akustischen Messungen.

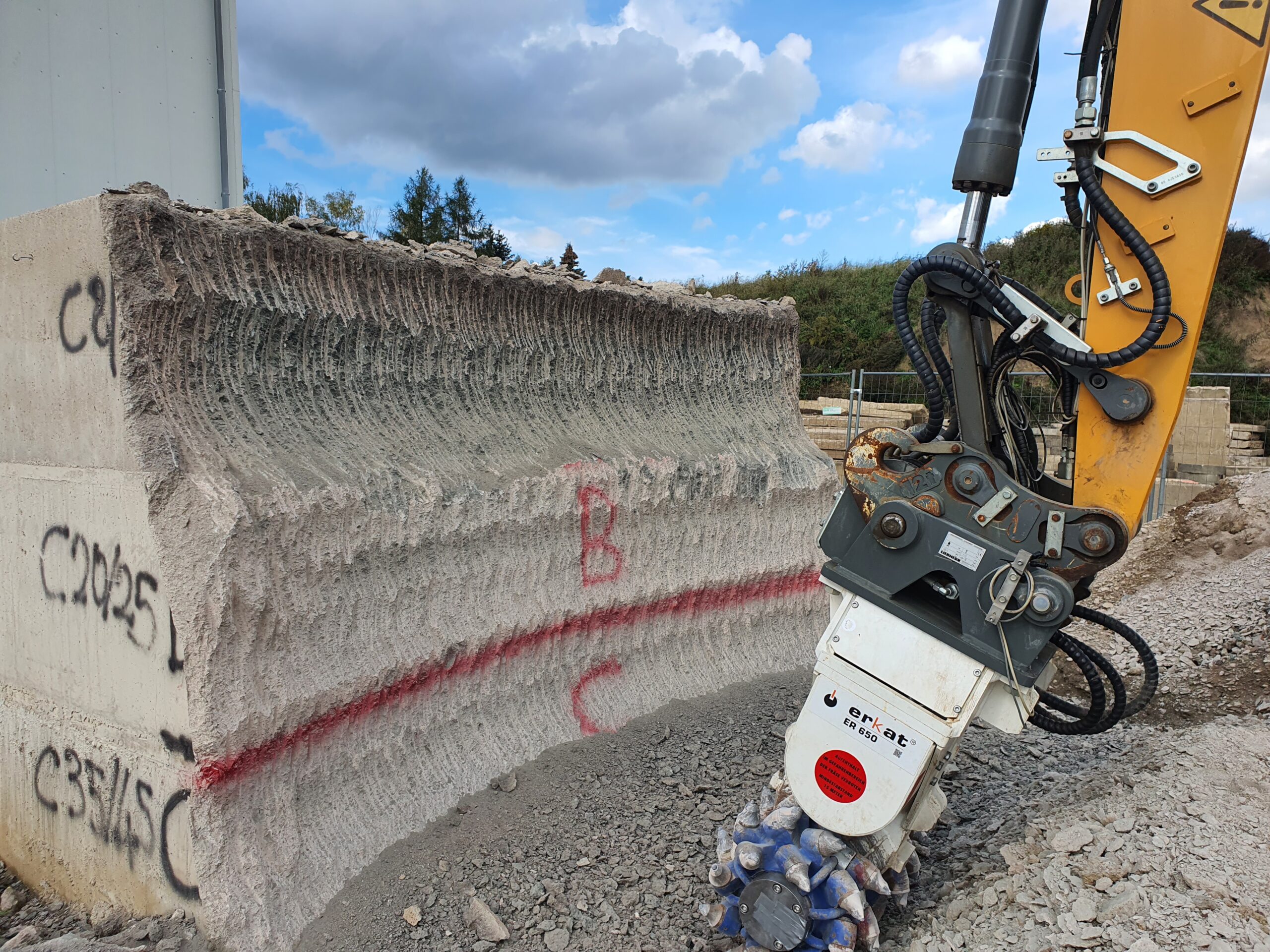
Mobiler Teststand Freiberg
Anbaufräse auf Massivbeton
Nachdem auf dem stationären Teststand der Funktionsnachweis der RockFeel-Meiselsensorik erbracht wurde, hat RockFeel 2021 ein erstes Funktionsmuster für eine 80kW-Anbaufräse ER650 hergestellt und an einem ca. 20m³ großen Probekörper aus drei verschieden festen Schichten Beton (UCS 15 |22|40MPa) getestet. Der nach komplexen Filterverfahren ermittelte Festigkeitskennwert RockFeel Strenght (RFS) zeigt eine deutliche Korrelation zur Betonfestigkeit UCS mit einer Auflösung von unter 10 MPa.
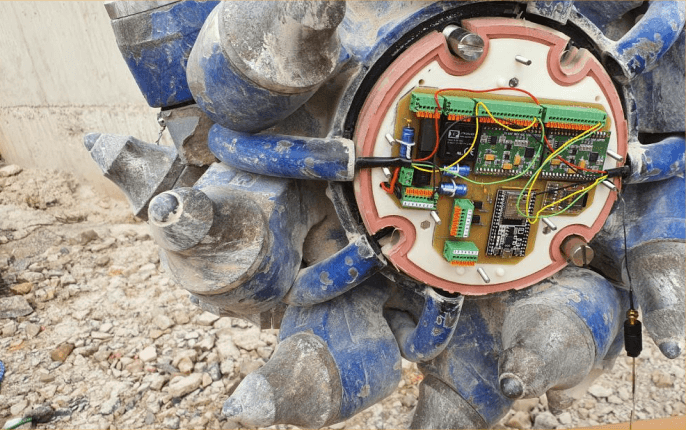
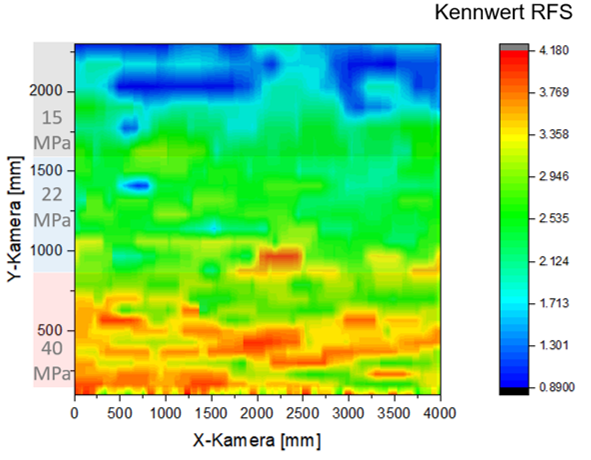
am Betonblock
Das Testgelände wurde uns von der LSTW GmbH aus Freiberg großzügig zur Verfügung gestellt, deren Fachleute auch den Betonblock gegossen haben. Den Bagger hat die B.I.V.. GmbH aus Freiberg sehr günstig bereitgestellt. Die Fräse wurde für die Tests durch die ERKAT PC Fräsen GmbH angepasst, um z.B. den Öldruck und den Drehwinkel beim Fräsen unmitelbar messen zu können und um Kabel von den Meißelhaltern geschützt zum Seitendeckel führen zu können, auf dem die Datenvorverarbeitung und drahtlose Übertragung auf einer gedämpft aufgehängten Platine erfolgt. Hierbei hat uns EPIROC durch wertvolle Hinweise geholfen, denn der erste Schuß hat getroffen, die Platine ist auch nach mehr als 80 Stunden aktiven Fräsens von 2021-2023 voll funktionsfähig. Die Elektronik wurde von Erik Börner und seinem Team am Institut für Bergbau und Spezialtiefbau der TU Freiberg entwickelt und umgesetzt.
Vielen DANK an unsere Partner!
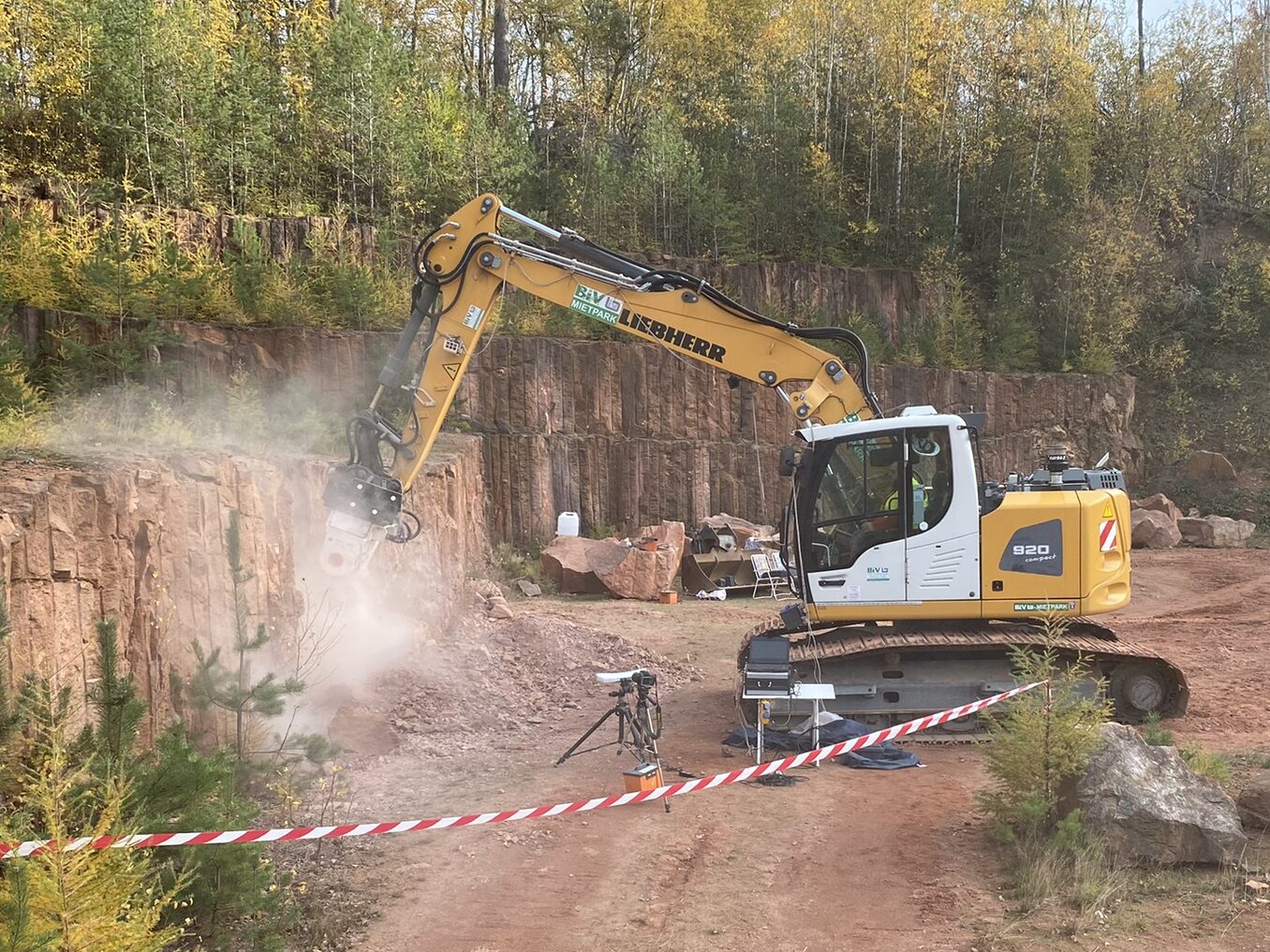
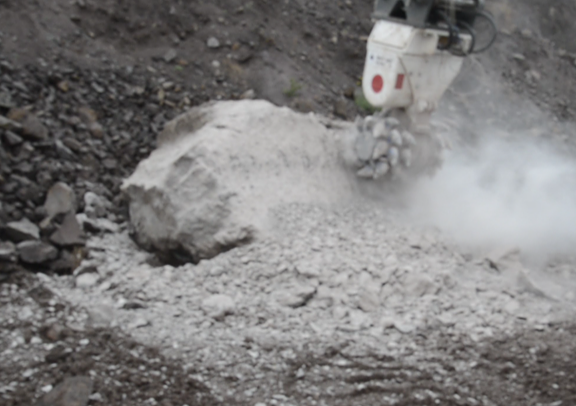
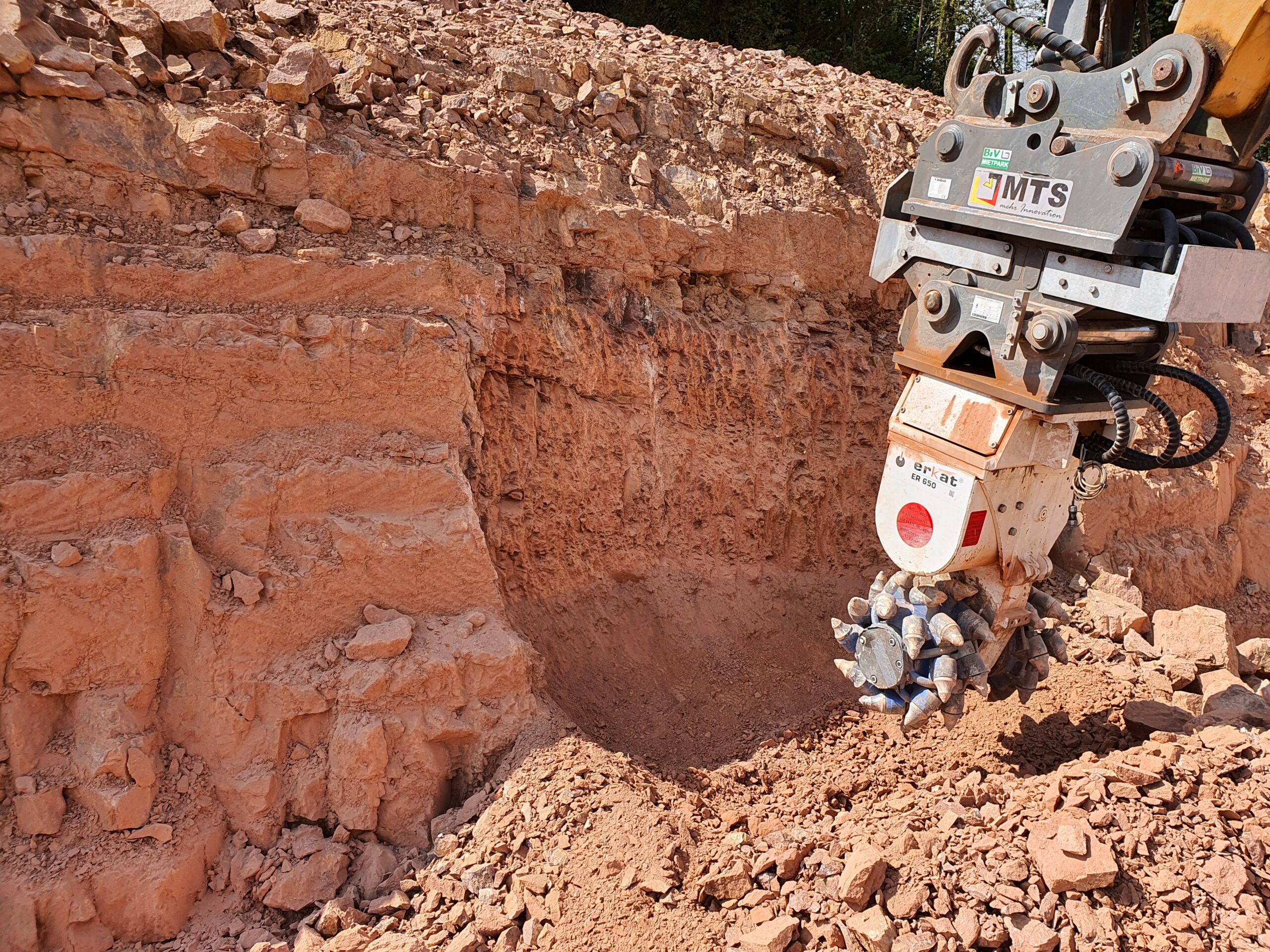
Tests in Steinbrüchen
Anbaufräse in Porphyr, Andesit, Sandstein, Quarzporphyrtuff
Nach der ersten Evaluierung anhand von Beton hat Rockfeel 2022 begonnen, seine Meißelsensorik an gewachsenem Stein zu verifizieren. Ziel war nun vor allem der Nachweis, dass die ermittelten Kennwerte zum einen konsistent sind – also am gleichen Stein bei geringer Variation reproduziert werden, zum anderen zur tatsächlichen Festigkeit des geschnittenen Materials korrelieren. Zu diesem Zweck wurden teils vor Ort Bohrkerne gezogen und gesteinsmechanische Untersuchungen nach einschlägigen DIN-Vorschriften durchgeführt. Dieser Nachweis ist gelungen.
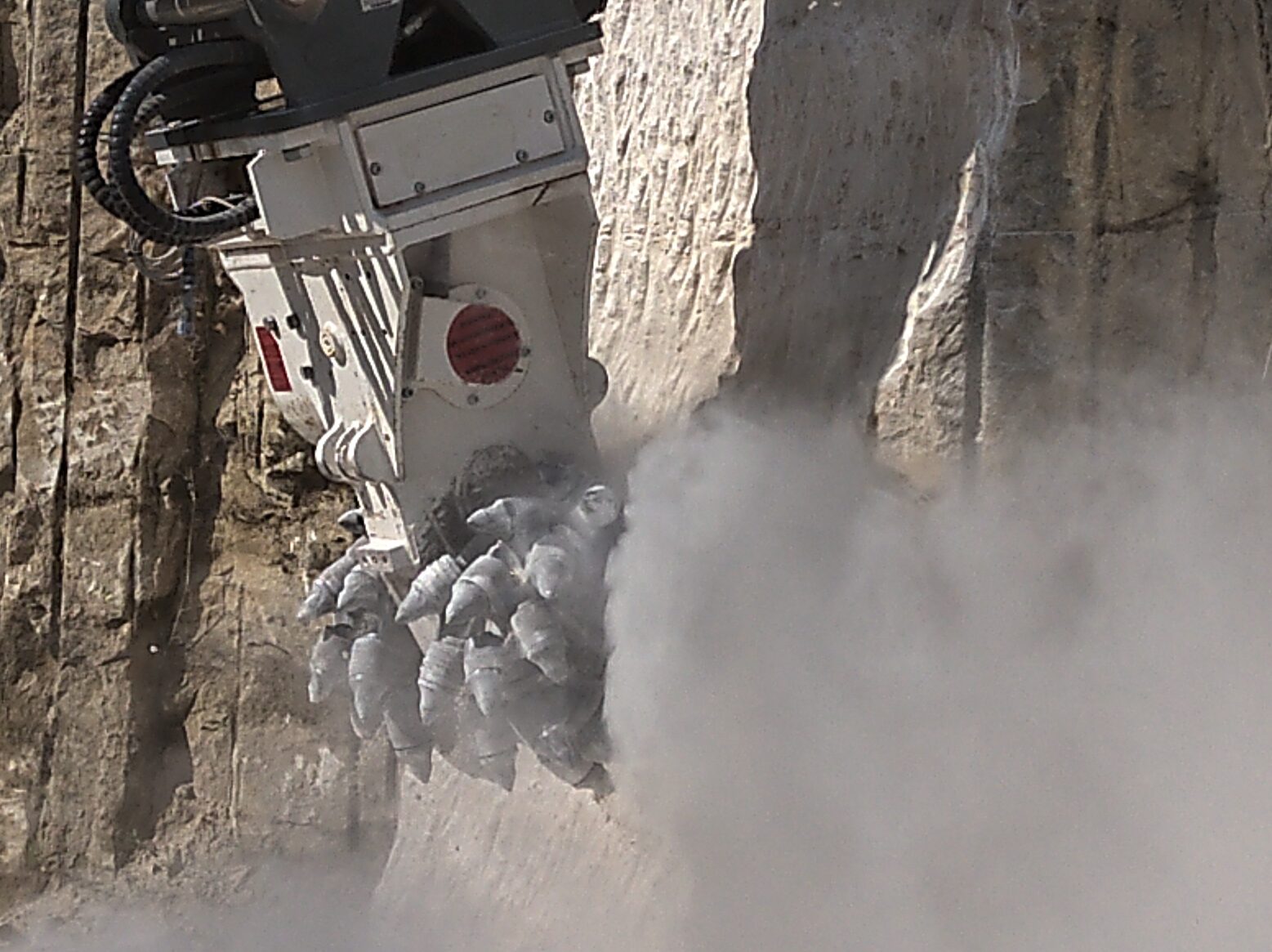
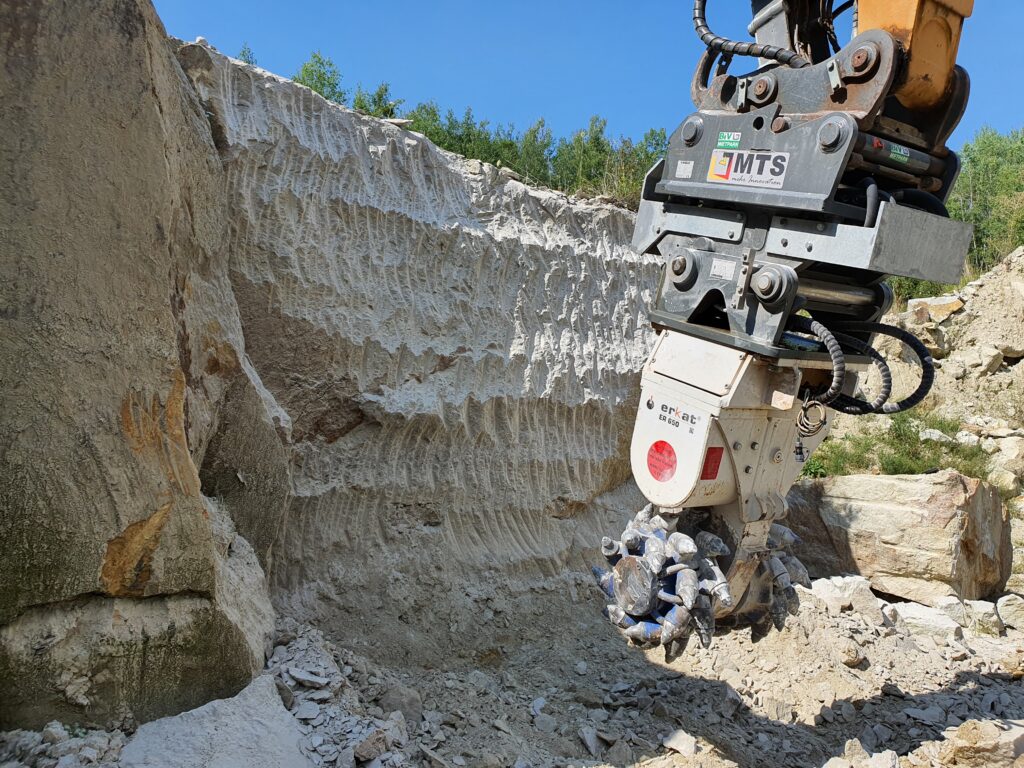
Auch hier haben uns regionale Bergwerksbetriebe unkompliziert und großzügig unterstützt. Wir bedanken uns sehr herzlich bei den Vereinigten Porphyrbrüchen auf dem Rochlitzer Berg, bei der Eiffage Infra Ost GmbH, den Sächsischen Sandsteinwerken und der Wilhelm Geiger GmbH & Co. KG für die Möglichkeit, an insgesamt fünf Betriebsorten Schneidtests mit unserem RockFeel-Sensorsystem durchzuführen. Das erweiterte Projekt wurde im Auftrag der EPIROC Deutschland GmbH durchgeführt, B.I.V. stellte einen schweren Liebherr Kettenbagger R926 zur Verfügung, der von verschiedenen sächsischen Transportspezialisten zwischen den Standorten transportiert wurde.
Diese Tests erweitern wir schrittweise um weitere typische Naturgesteine.
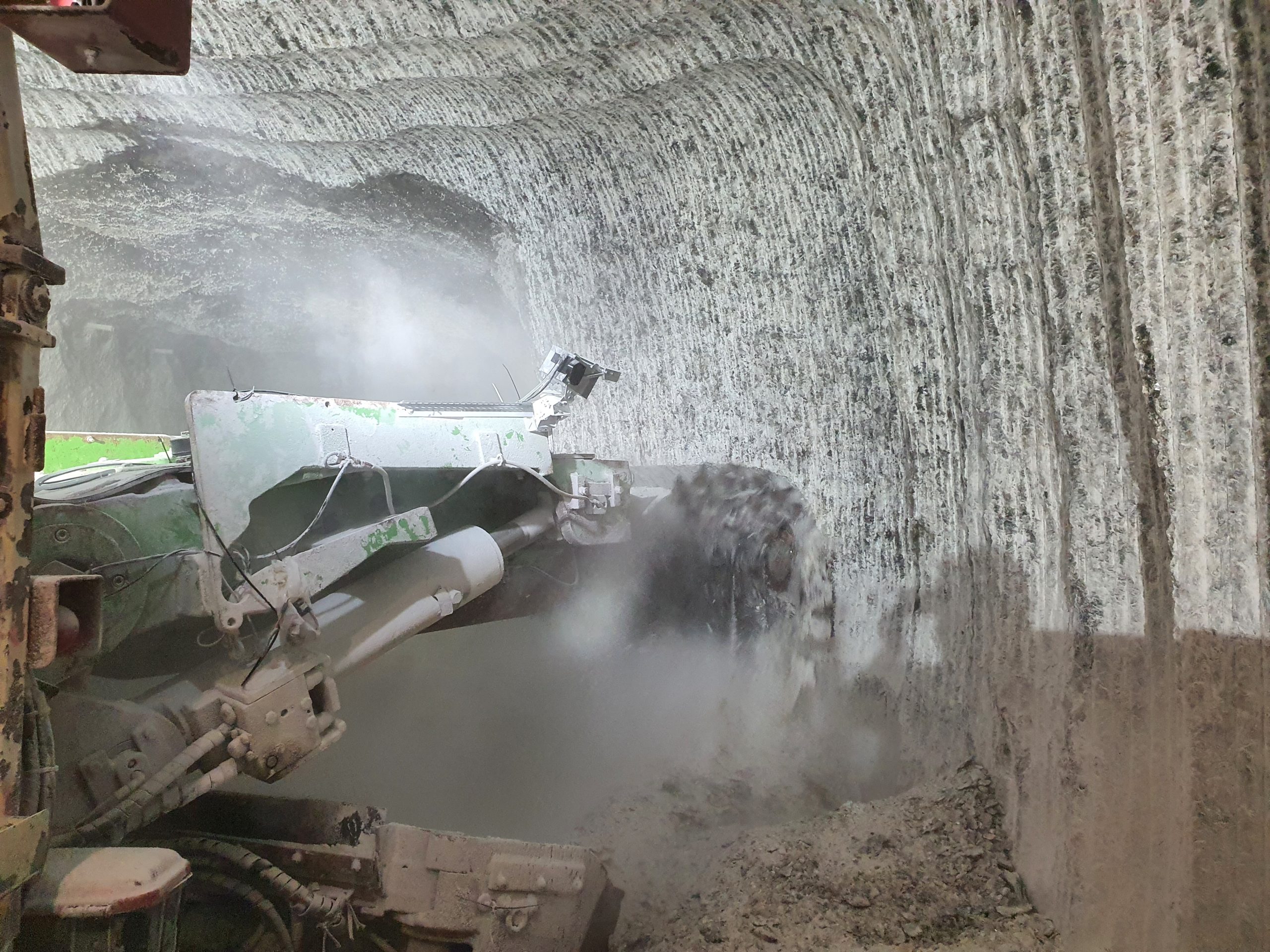
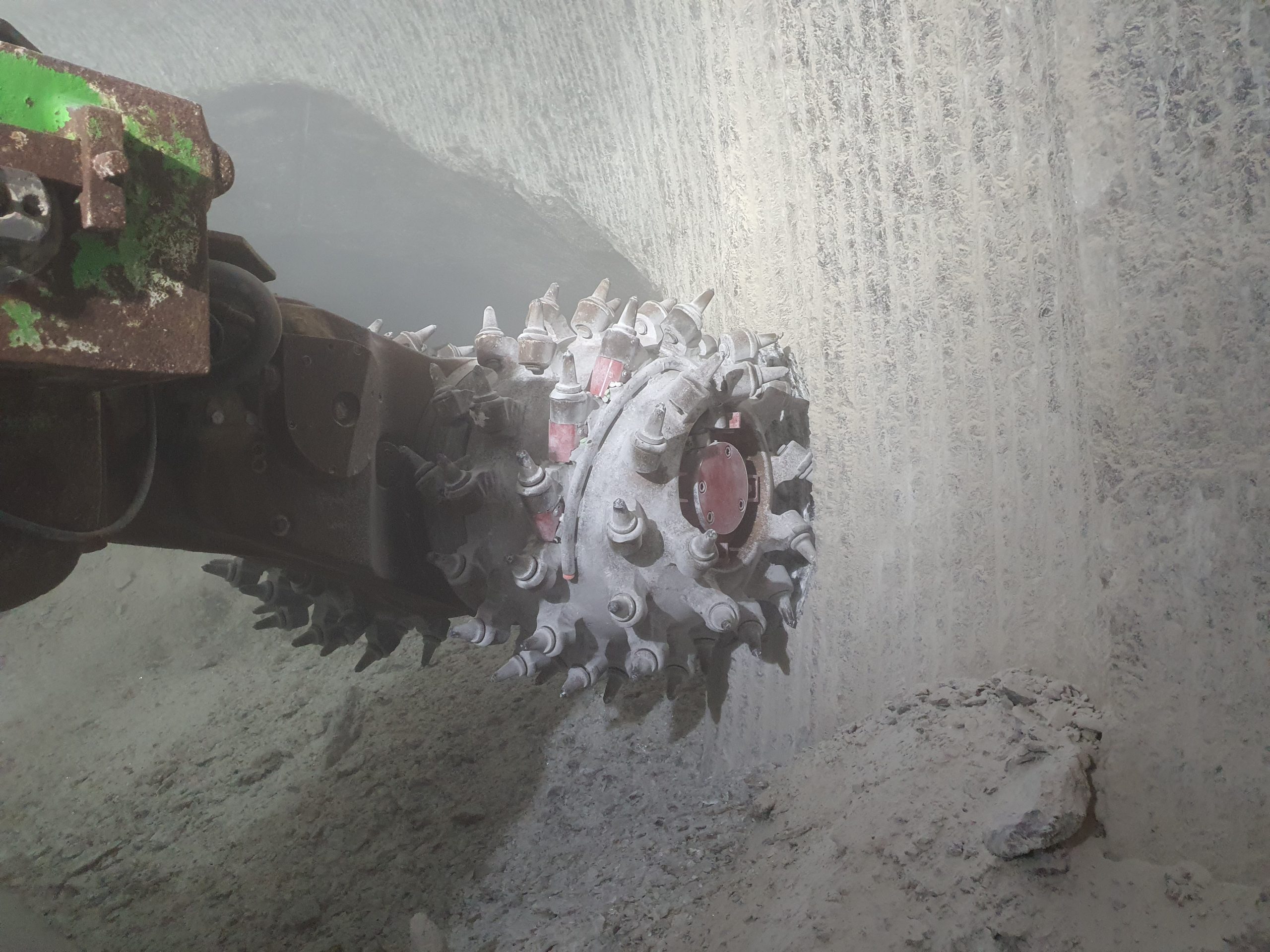
Tests untertage
Teilschnittmaschine im Steinsalz
Nach der erfolgreichen Evaluierung in verschiedenen Steinbrüchen wurde der Prototyp auf einer Teilschnittmaschine der Südwestdeutschen Salzwerke AG im vergleichsweise weichen Steinsalz untertage gestestet. Der untertägige Abbau birgt ganz eigene Herausforderungen.
Die ermittelten Kennwerte waren auch auf der erheblich größeren und stärkeren Maschine und mit langen Meißeln, die erheblich tiefer ins Gestein eingreifen, konsistent, konnten also bei geringer Variation an gleichartigem Material reproduziert werden.
Dank der großzügigen Bereitstellung einer im aktiven Betrieb befindlichen TSM konnte auch der CWA-Prototyp zur Verschleißüberwachung und ein erster Aufbau eines Asistenzsystems zur Unterstützung des Bedieners bei starker Staubentwicklung getestet werden, die in diesem und anderen Einsatzfeldern dieser Geräte häufig auftritt und der Produktivität deutliche Grenzen setzt.
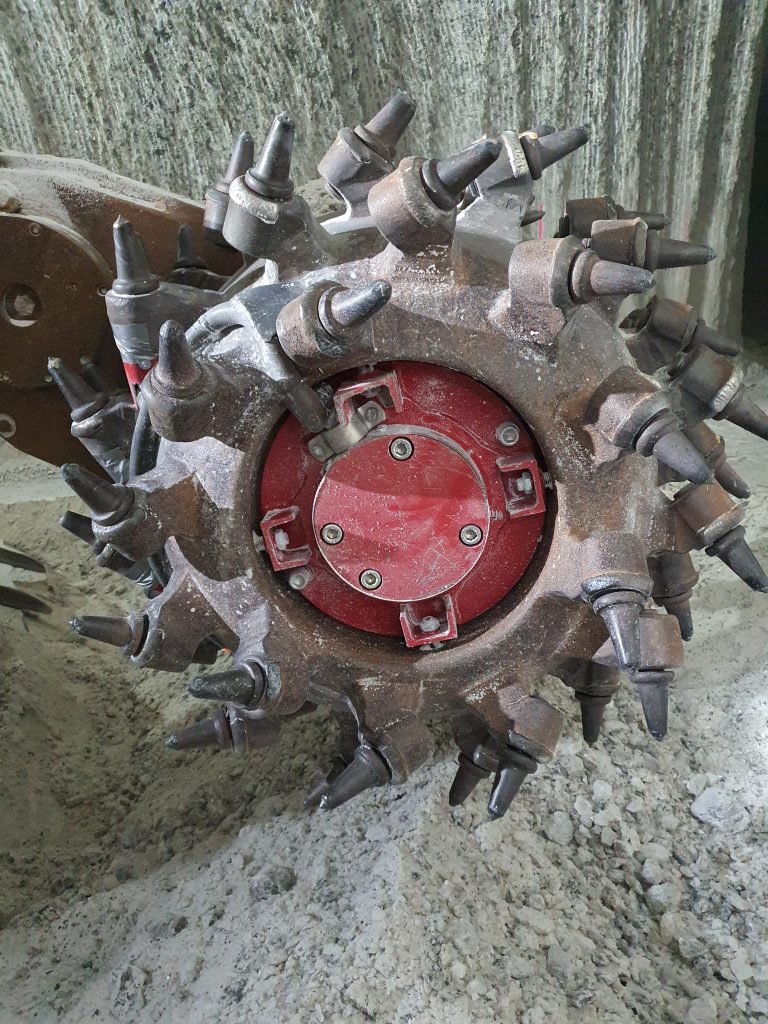
sd